PAPER N0. 11 SUMMARY
Applying Drive Specifications to Systems Applications: Part III Position Regulation
2002 IEEE IAS Annual Meeting
Brian Thomas Boulter
Applied Industrial Control Solutions LLC
4597 E Sprague Rd.
Independence, OH, USA 44131
© ApICS ® LLC 2000
Abstract- In web handling and strip processing lines, position loops are used to regulate dancers, accumulators, cutting shears, and for motion or positioning control in many other applications. Depending on the requirements of the application, a fast responsive torque regulator may or may not be required. This paper provides guidelines for the useful interpretation of AC/DC drive performance specifications as applied to positioning applications, from a drive system’s application perspective.
I. Introduction
As noted in [3], [4] the technical climate in today’s drive systems business markets has been inundated by drive vendor claims of ever improving drive performance specifications. The objective of this report is to bring those performance specifications that apply to positioning and motion control applications into technical focus, and provide the reader with a basis for correctly interpreting them from a SYSTEMS /APPLICATIONS perspective. A future paper will address performance issues associated with "cascaded" and "parallel", tension regulation schemes. Part I [3] dealt with speed regulation issues, Part II [4] dealt with torque/current regulation schemes.
It is hoped that the reader will walk away from this presentation with the tools required to sift through a given drive’s performance specifications, and glean from them those points that are truly of importance to the position/motion control application in question.
Paper Overview
The paper is divided into four sections. The first section is composed of this introduction and the paper nemenclature, the second section defines a set of useful terms, the third section defines the most important drive specifications with respect to positioning and motion control, and methods of determining these criteria for a given drive system. A set of observations and conclusions are presented in the fourth section
IV. Conclusions
The performance of industrial control position and motion control applications are occasionally limited by the drive technology that is used. This typically occurs when the per-normal inertia, and per-normal storage of the system are small, and the mechanics of the system are very stiff, and well designed with minimal backlash and friction. Guidelines presented in this paper and in [3], [4] empower the cognizant control system engineer to make intelligent vendor choices when procuring a drive, based on the needs of the application in question.
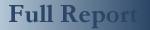
|