PAPER No. 1
Matrix Interpolation Based Self-Tuning Web Tension Regulation
1995 International Web Handling Conference
Brian Thomas Boulter
Applied Industrial Control Solutions LLC
4597 E Sprague Rd.
Independence, OH, USA 44131
© ApICS ® LLC 2000
ABSTRACT
A self-tuning control scheme is proposed for tension regulation in a web handling system. A matrix interpolation based computationally efficient self-tuning method is first described. The frequency domain model of the plant is then derived. Simulations of the on-line tuning are presented and a comparison is made with current tension regulation methods. The paper closes with a discussion of cognizant implementation issues.
INTRODUCTION
Web tension regulators are typically implemented with a PI controller as shown in Figure 4. The PI parameters must be tuned to provide a stable and satisfactorily responsive system for the entire spectrum of web material processed through the tension regulated section of the process. In processes where there is a large range in web cross-sectional areas this tuning approach results in a closed loop system that is less than optimally tuned for most of the web material processed through the system and optimally tuned for only a small range of web material. At the time the line is being commissioned the usual tuning approach is to process product with the maximum available and minimum available cross-sectional areas. The regulator proportional and integral gains are empirically adjusted so that acceptable tension regulation is realized. A service engineer remains on-site to observe the behavior of the system during normal production runs. Should any instability be encountered during this "baby-sitting" period re-tuning (or "tweaking" as it is affectionately called) is conducted to ensure that the system will be handed over to the customer in a tuned state that minimizes down-time during normal production runs.
While it is highly desirable to analytically derive an algorithm for pre-tuning the PI regulator parameters based on customer supplied web and plant parameters, unknowns such as web damping, friction, and roll slippage make the derivation of such an algorithm difficult. The usual approach is to heuristically tune the PI controller on-site as described previously. Should instability occur when web material with extreme cross-sectional areas is processed through the system the need arises to re-tune the loop. A better approach would be to provide a self-tuning regulation scheme that obviates the need for empirically finding a single unique set of stable tuning parameters for the entire range of products processed through the system.
To this point in time adaptive and/or self-tuning regulation schemes have not been considered for web handling systems. This fact can be attributed to the complexity of the existing time-domain algorithms, and the associated hardware and software implementation difficulties. K. J. Astrom in [12,13 and 16] and I. D. Landau in [17] summarize a variety of self-tuning regulation approaches using PID and feedback/feedforward techniques. In general most of these approaches are computationally complex. Knowledge based systems have been implemented utilizing fuzzy logic and other rule based approaches with some success [19, 20, 21]. These approaches require customized rules based on the given application, and are not practical for systems that are required to be tuned "out-of-the-box" with minimal customization. Recent developments in the field of self-tuning control have led to some exploration of frequency domain loop shaping self-tuning algorithms. These algorithms are based on iterative procedures that minimize a cost function [1,5 and 10]. With the exception of the rule-based algorithms, the algorithms used in the above adaptive and/or self-tuning regulation schemes do not lend themselves well to a-priori computation of the time required to converge to a solution. In general, the above self-tuning techniques are not computationally efficient enough, nor is the algorithm execution time predictable enough, to be used in self-tuning regulation (STR) for web transport systems. Distributed Control Systems (DCS), today’s standard industrial control platform, are implemented with constrained computational resources requiring efficient algorithms with predictable execution times.
The STR method proposed in this paper is neither complex nor difficult to implement. It identifies controller parameters through an interpolation algorithm that utilizes a desired open loop frequency response and frequency domain information from the plant. The core of the algorithm is expressed in finding the least squares solution of a system of linear equations. It is, therefore, extremely efficient and predictable. For these reasons this particular STR algorithm is attractive for self-tuning implementations in a DSP based DCS platform. The self-tuning algorithm is extensible and can be extended to any SISO control scheme.
To introduce the reader to the proposed STR algorithm and this particular implementation, the self-tuning algorithm is derived in Section 2. A web transport plant is described in Section 3. together with its associated mathematical model. The simulation results of both a typical web tension regulator and the proposed regulator are presented in Section 4. To clarify the benefits of on-line tuning based on a measured plant frequency response as opposed to of-line tuning based on the frequency response of an analytically derived transfer function, Section 4 presents a comparison of the these two approaches. A discussion of implementation considerations can be found in Section 5.
SELF TUNING REGULATION ALGORITHM
Background
The most prevalent method of SISO industrial control system design in use today is the loop shaping approach. This approach hinges upon the design of a controller that satisfies a set of loop gain specifications. It requires the derivation of an approximate linear plant model. To arrive at an acceptable design, skill and experience are often required. The design procedure is typically carried out in a cut and try manner. The tools most commonly used to perform the design are Bode and/or Nichols plots. A new algorithmic loop shaping design approach is described in this section, which reduces the design problem to solving a set of linear algebraic equations.
Given that the proposed design algorithm can be coded and executed autonomously by a computer, the possibility of performing loop shaping SISO controller design on-line in an autonomous self-tuning regulation scheme becomes feasible. The purpose of this paper is to describe one such scheme. Figure 1 is the block diagram of the proposed STR scheme.
An FFT algorithm is used to obtain the plant frequency response . The STR algorithm makes use of the obtained frequency response and the loop shaping algorithm described in the following section to update the controller parameters. The anti-windup switch and stimulus block are implemented to provide a frequency rich autonomous stimulus to the plant for the purpose of obtaining a meaningful plant frequency response and are unique to web tension regulation.
A New Loop Shaping Algorithm
A popular approach used in loop shaping design translates desired closed-loop performance specifications to constraints on the loop gain. For example:
Low Freq. Gain = 50 [db] at 0.1 [rad/sec]
Crossover Freq. = 8 [rad/sec]
Phase Margin
High Freq. Atten.= -40 [db] at 200 [rad/sec]
are typical specifications for a closed loop system with a step response time to peak of approximately 0.375 [sec], approximately 10% overshoot, negligible steady state error to a step, and good high frequency noise rejection and stability robustness. They can be considered typical for web tension regulation schemes.
While the above constraints are typical they are by no means all inclusive. A control system designer may want to design a controller such that non-typical constraints are accommodated. For example, stop band attenuation or pass band amplification at particular frequencies may be desired. The algorithm that is developed in the following derivation automates the design of a regulator to satisfy any such set of loop gain constraints. It minimizes the error, in a least squares sense, between any set of loop gain constraints and the loop gain resulting from the product of the measured plant frequency response and the tuned regulator. The design problem is formulated as a matrix interpolation problem. An important characteristic of the algorithm that separates it from current loop shaping approaches is that it is not iterative. The interpolation constraints are satisfied with controller parameters obtained by solving a system of linear equations.
Algorithm Derivation:
A controller with a frequency response of can be designed for a given plant frequency response such that a desired loop gain is realized. That is:
(1)
Let:
Where , are the controller numerator and denominator polynomials respectively. (1) can be expressed as:
(2)
or:
(3)
The objective of the new STR algorithm is to find coefficients of the controller such that equations (1) thru (3) hold at a set of chosen frequencies. The derivation of the STR algorithm is performed in two steps. The first step is to obtain a matrix equation based on (3) but expanded and expressed in terms of a finite set of independent frequencies. The second step is to perform matrix operations on the resulting equation such that a system of linear equations of the form is obtained.
Step 1) Represent (3) in terms of a finite set of independent frequencies
For the example loop gain constraints given previously, the desired loop gain frequency response can be expressed as a vector of complex scalars taken at l frequencies:
(4)
The plant frequency response can be obtained via an FFT as a vector of complex scalars:
(5)
The FFT algorithm must output a vector of complex scalars that is composed of elements taken at the same frequencies as those chosen for (4).
Working with a controller representation in the s-domain, a regulator structure C(s) is chosen for the given application. It must be proper.
(6)
The regulator can be expressed in matrix form in terms of its coefficients as:
(7)
Let be the vector containing the parameters of the controller
(8)
and let:
(9)
(7) can now be expressed in the frequency domain as:
(10)
The plant frequency response and the desired loop gain response can be represented as , a 2 row matrix with l columns corresponding to the number of frequency points specified in (4).
(11)
Eq. (3) evaluated at may now be represented as:
(12)
Where: is a 1 x (m+n+2) matrix
is an (m+n+2) x 2 matrix
is a 2 x l matrix
Step 2) Perform matrix operations on (12) so that the resulting matrix equation is in the form .
Expanding yields the following matrix
(13)
may be represented as:
(14)
Where:

Given that the lth entry in is -1 (12) can be expressed as:
(15)
where:
(16)
From (15) we obtain:

and finally:
(17)
The matrix equation (17) is now in the desired form . (17) can now be expressed as:
(18)
Solving the set of linear equations in (18) yields the tuned regulator coefficients . is rarely square therefore a pseudoinverse is used to find the least square solution of the set of linear equations. Obtaining the least squares solution of (18) may also be expressed as finding the best fit of controller parameters such that the least squares error between the desired loop gain and the loop gain resulting from the controller design is minimized. The Moore-Penrose pseudoinverse algorithm is a suitable algorithm for this application and is described in [11]. A second consideration is that and are complex matrices. To avoid the necessity of writing code for finding a pseudoinverse for a matrix with complex elements, [15] provides a method whereby the coefficients can be found by dividing and into real and imaginary parts as shown in (19). The pseudoinverse may now be obtained from a matrix with all real numbers, making the coding considerably simpler.
(19)
The algorithm may be summarized as follows:
1. Provide a vector of desired loop gain frequency response data ( ) at l frequencies.
2. From a set of measured input output data, taken from the plant on-line, compute the plant frequency response vector ( ), using an FFT algorithm, at the same frequencies as .
3. Substitute and into (13) and obtain the and matrices using (14).
4. Substitute the and matrices into (19) and solve the linear system of equations using a suitable pseudoinverse algorithm. The solution yields the controller parameters.
5. If the implementation is in a discrete environment, calculate the z-domain controller coefficients using a suitable transformation technique and update the controller.
A short discussion regarding controller structure selection:
The choice of the controller structure is application dependent. Care must be taken to select a controller with an order high enough to satisfy the given regulation requirements. As stated previously, the proposed STR algorithm achieves the best possible fit between the desired loop gain and the actual loop gain. Often this results in approximate pole zero cancellation. Approximate pole zero cancellation has been used for many years in industrial control systems. For example the motor electrical time constant is canceled with the zero of a PI controller in motor current loops, many other examples could be given. This approach is entirely acceptable when the values of the plant poles and zeroes do not change significantly (as is the case for a given product in web transport systems). If the plant poles and zeroes do change, an STR algorithm will be employed to adjust the controller parameters to compensate for the changes.
For this application a fourth order controller structure, as shown in Figure 6, provided adequate regulator designs. This choice was made with the a-priori knowledge that there are three dominant poles in the plant transfer function, as will be shown in the following section, and that making the regulator an order higher than the plant order provides on-line regulator tunings that meet low frequency gain specifications. In the following section it will be shown that if a PI regulator is used the system modeled in this paper is type 2 at stall, a condition where tension is applied to the web but the line speed is zero. This is due to an inherent integration in the plant, it will not however be type 2 when the web material is moving through the tension zone.
MODELING OF A WEB TRANSPORT SYSTEM
Plant Description
A physical representation of the plant shown in Figures 4 and 5 is shown in Figure 2. The motor and gear-box have been omitted. Assuming that:
1. Unstretched web is introduced into the tension zone.
2. Bridle No. 1 is an ideal speed regulator.
[6 - 8] show that for small signal analysis, change in tension in the tension zone (the tension zone is the length of web between the speed regulated bridle and the tension regulated bridle) can be modeled in the Laplace domain by (20) a commonly used tension model in web analysis.
(20)

|
The change in web tension in the tension zone [N] |
E |
Web modulus of elasticity [N/cm^2] |
A |
Web cross sectional area [cm^2] |
L |
Web length [m] |

|
Velocity of feed roll [m/sec] |

|
Velocity of exit roll [m/sec] |

|
Tension in the web entering the tension zone. |
Modeling the motor inertia and driven roll inertia (reflected through the gear-box to the motor shaft) as a lumped inertia J, a block diagram of the plant (Figure 3 can be constructed using (20). is a constant that converts motor rotational speed to linear line speed. is a constant that converts web tension to a torque reflected through the gear box and felt at the motor shaft. represents the torque produced by the motor. is the coefficient of viscous friction. is the web-damping modulus.
The inner speed loop will be seen by the STR in Figure 5 as an integral part of the plant that is being controlled, therefore all references to the plant from this point forward will assume the speed loop to be lumped with the physical plant into a "super plant" combining the dynamics of both the speed loop and the physical plant.
Assuming that: 1) The tension in the web entering the tension zone is zero; 2) the system speed reference is constant; It can be shown that the transfer function from the output of the tension regulator to the tension feedback in Figure 4 is:
(21)
where:
J : Lumped Bridle/Motor inertia [Kg m^2]
: The inner speed loop PI proportional gain term
: The inner speed loop PI lead frequency [rad/sec]
D : The driven roll diameter [m]
GR: The gear ratio



Note that (21) does not include web-damping ( ) or viscous friction ( ). If we include the transducer filter (see Figures 5 & 6), (21) becomes:
(21.a)
Of particular interest is the behavior of the tension loop at stall. The transfer function of the control system in this condition can be found by setting V 1 (the line speed) to zero in (21). First multiply the numerator and denominator of (21) by and set = 0, this yields:
(22)
From the authors experience of known system behavior the third order denominator in (21) can be factored into the form :
(23)
Where is known to be an approximately linear function of line speed V 1 and is known to be a function of . In underdamped systems approximates the frequency at which energy is exchanged between the spring of the web material and the lumped inertia J. represents the damping factor of the resonant pole pair associated with .
Let : ; ; 
: The inverse of the line velocity time constant
: The closed speed loop bandwidth (w/o web)
R : The web/inertia natural frequency
It can be shown that:
(24)
The equations in (24) are satisfactory approximations of the exact values providing which is reasonable for all practical web transport systems.
Observations concerning the factored transfer function
Some interesting observations can be made from (24) namely;
- The center frequency
of the open loop 2nd order pole pair increases with a corresponding increase in the speed loop bandwidth.
- Damping of the open loop 2nd order pole pair

increases with speed loop bandwidth.
In addition to the need for zero steady state error to a ramped speed reference, the above two observations provide additional impetus for the inclusion of a speed minor loop in any tension regulation scheme.
From the tension loop control system design perspective, the value of in (24) is critical since the final design will depend on the installed system having a real or complex pole pair. The worst case system operating condition is at stall ( = 0, = 0, ) and it is in this condition that a web tension loop is typically tuned. Unfortunately in real applications the value of is affected by non-modeled parameters such as web-damping, mechanical friction, roll slippage, and in the case of films and paper, temperature and humidity. To summarize, the inability to analytically identify in (24) is the main contributing factor to the need for heuristically tuning web tension regulators in the field.
It is also clear from (24) that the frequency varies as a function of E, A, L and J. In general it is obvious that a system with no STR mechanism needs to be tuned for stable operation with the worst case operating parameter set (quite often in and of itself hard to identify) and that for other operating parameter sets the system is running in a stable but less than desirable condition.
SELF TUNING WEB TENSION SCHEME & SIMULATION
Self Tuning Web Tension Regulator
To clarify the difference between the traditional web tension regulation approach and the proposed approach detailed block diagrams of the two schemes are presented (Figures 4 & 5.).
Figure 4 represents a typical tension regulation scheme as used in industry today. is the outer tension loop vernier contribution to line speed reference. It can be shown that the use of a PI regulator for speed regulation results in a type 2 inner speed loop, a necessity for web transport systems where there must be zero steady state error to a ramped speed reference (for acceleration and deceleration of the process line). A transducer filter is typically employed to filter unwanted high frequency noise. For this application the corner frequency of the transducer filter was set at 20 [rad/sec], a typical value.
Figure 5. is a representation of the proposed STR algorithm as implemented in the simulation described in this paper. The tension Loop PI regulator is replaced with an STR regulator, an anti-windup switch, a stimulus switch and an autonomous supervisory controller. The function of the anti-windup switch and the stimulus switch is explained in the logic sequence at the end of this section. The use of a PI controller for the inner speed loop in the STR regulation scheme is desirable due to the need to ramp up to an operational line speed with zero error to a speed ramp, as described previously, as well as the need to jog the bridle for threading new web material into the process line.
From Figure 1. it can be seen that a supervisory controller is implemented to provide the sequencing logic required to execute the STR algorithm. The logical sequence used in the simulation performed in this paper is as follows:
1. Set the anti-windup switch. (set the input of C(s) to zero effectively disabling C(s)).
2. Provide a step stimulus to the plant input.
3. Collect a set of input/output plant data and perform an FFT to obtain P(j wi)
4. Initiate the STR loop shaping algorithm, obtain a set of controller parameters, and update the controller.
5. Continue stimulus and monitor the feedback and tension reference. Turn of the stimulus when the feedback matches the reference (error = 0). Release the anti-windup switch and re-enable the re-tuned controller.
In other applications this algorithm need not be adhered to. The more traditional STR approach may also be implemented. That is, a continuous FFT may be generated from normal plant operational stimulus/response data and the controller updated periodically without the need for the anti-windup switch and an autonomous stimulus. However this is only feasible if the harmonic content of the normal operational stimulus is adequate enough to obtain a meaningful FFT. In applied tension regulation schemes the tension reference rarely changes and the feedback is always constant. This results in the need to provide an autonomous stimulus, as described above, when self-tuning is desired.
Simulation Set-up
The simulation was performed using SIMULINK and MATLAB. Viscous friction, web-damping, tension feedback white noise and line speed white noise were included to provide realistic unmodeled dynamics. The objective of the simulation was two-fold; 1) To demonstrate the ability of the self-tuning algorithm to satisfactorily re-tune the controller 2) To demonstrate the advantage of on-line self-tuning based on the measured frequency response of the plant as opposed to of-line tuning with the STR algorithm using the transfer function model (21.a) to obtain a theoretical plant frequency response. Space limitations have restricted the presentation to a single cross-sectional area. Simulation has shown however that the algorithm generates satisfactory regulator tunings for any changes in web parameters. The simulation set-up parameters are presented in Table No. 1.
A SIMULINK masked s-function performs the on-line FFT and executes the self-tuning algorithm to provide the new controller parameters. During the self-tuning process the system is stimulated with a small speed reference step as described in section 2. Care was taken to ensure that web tension was reasonably bounded during this period. To prevent regulator windup during the plant stimulus process, the input to the tension regulator is forced to zero by setting the anti-windup switch.
For the first simulation set (Figure 6 through 8) the self-tuning system was initialized with a set of poorly tuned controller parameters. Two tension steps of 5 [sec] duration (from 0 to 10 [sec] in Figures 9 and 12) were followed by a 10 [sec] data collection and regulator tuning period. After which the re-tuned STR response to three tension steps of 5 [sec] duration was obtained. Figure 6 represents the theoretical plant frequency responses obtained with the use of (21.a). The plant frequency responses obtained on-line with the FFT are shown in Figures 7. These plots are presented with probabilistic bounds of 1 standard deviation as described in [18] pp 1-21,22. This presentation technique is similar to that described in [1] section 2.
A second simulation (Figure 9) was performed to obtain a comparison between a regulator tuned of-line with the STR algorithm using transfer function (21.a) to obtain the plant frequency response (from 0 to 10 [sec]) and a regulator tuned on-line with the STR algorithm (from 20 to 35 [sec]). The on-line tuning process was the same as that used above.
For the purpose of comparing the STR’s responsiveness to that of a standard PI controller, a second system implemented with a PI tension controller was configured with the same plant. The PI controller was tuned heuristically based on observed simulation tension step responses (much the same as would be done in the field). Figure 10 represents a collage of step responses that provide a clear comparison between the two regulation approaches. The Following final PI tuning parameters were used: Kt = 0.06, = 2;
Simulation Observations
Figures 9 demonstrates the STR algorithms ability to tune on-line in the presence of unmodeled dynamics for a low cross-sectional area. The higher than desired overshoot can be attributed to inaccuracies in the on-line measured FFT plant frequency response. It was observed that relatively accurate plant frequency response data, as shown in Figure 7, is critical to the success of the application of the described self-tuning algorithm. Factors impacting the quality of the estimated plant frequency response are: 1) Sample Time (high frequency response). 2) The sample length (low frequency response). 3) The choice of FFT windowing algorithm (transient disturbance and noise rejection). 4) The choice of smoothing algorithm (noise rejection). 5) Harmonic content of the input stimulus (overall frequency response). These topics have been covered in [1], [9], [10], and [14]. Adequate performance of the STR algorithm on-line will depend on making appropriate choices in 1) through 5) based on the given application and the desired loop gain.
Simulation results also indicate that the choice of frequencies used in the generation of L(jw) and P(jw) govern the quality of the final self-tuned regulator design. Care should be taken to provide frequencies low enough to generate a meaningful estimation of the plants low frequency response yet high enough to provide for adequate compensation of high frequency underdamped modes.
Figure 9 shows clearly that of-line tuning using the approximate linear plant transfer function (21.a) to derive the estimated plant frequency response resulted in unsatisfactory loop response. This can be attributed to the unmodeled dynamics present in the simulated system but not accounted for in (21). However by generating the frequency response of the plant on-line (including the unmodeled dynamics) the STR algorithm was able to provide a regulator tuning which adequately compensated for the included unmodeled dynamics.
Finally, Figure 10 shows that the STR algorithm configured regulators that realized a significant improvement in responsiveness over the standard PI design.
IMPLEMENTATION ISSUES
The object of good tension regulation in a web transport system is to produce good product. In the metals and film/plastics industries any excessive deviation in tension typically results in product that must be scrapped. Since the stimulus required to obtain a meaningful plant frequency response with an FFT will, in these industries, result in material that must be scrapped it follows that self-tuning be performed seldom and generate a minimum of waste material (Quite often, in these industries, a process’s profit margin is tightly linked to the amount of scrap material produced in a given time period ). For these industries the application of the described STR requires some thought and planning. If it is possible to excite the web in a stall condition, waste can be minimized. Applications in the metals industries that would meet this criteria, include rolling mills and tension levelers.
Rolling mills are employed in the metals industries to reduce the thickness of a web of metal and at the same time achieve a significant increase in hardness. This is accomplished by a combination of squeeze force acting on the web through a pair of extremely hard work rolls, and the stretching of the web with tension regulators either side of the work rolls. STR tuning could easily be accomplished at stall, after threading, but before the web is ramped up to line speed. The length of web in a typical reversing mill is only about 20 - 30 [ft]. Rolling mill operations typically scrap threaded material so there would be no increase in scrap material using the STR algorithm for tuning in this application.
In the metals industries, web that has been annealed in a furnace is pock-marked with surface deformities that are the direct result of the annealing process. A tension leveler is used to apply controlled strain at the web surface to effectively remove the deformations. The input and output of the leveler are speed regulated bridles (the "drag" and "drive" bridles) operating with slight differences in speed reference. The regulators either side of the "drag" and "drive" speed regulated bridles are tension regulated to minimize tension disturbances inside the leveler. This configuration, like the rolling mills described previously, may also be tuned with the STR algorithm at stall, after threading, but before ramping the process line to line speed. Waste would be minimized.
It would not be practical to initiate the STR algorithm for tuning tension regulators in the furnace sections of continuous annealing lines. Continuous annealing lines, as implied by their name, run continuously. A welding and/or web stitching machine is used to create a continuous web from many different product coils. These lines are only stopped when a breakdown occurs or when maintenance must be performed. Knowing that about 30 [sec] of data is required to obtain a meaningful FFT of the plant and that annealing lines operate at running speeds around 600 [ft/min], approximately 300 [ft] of material will have to be scrapped. For lines that run a wide range of products with relatively short lengths (in the range of thousands of feet) a substantial reduction in profitability due to scrap will be realized if the STR algorithm is employed.
Some industries process web where product quality is not sensitive to tension deviations. In these industries good tension regulation is required to minimize tear and product bunching on speed regulated process drive rolls. At low line speeds bunching and tearing is not problematic. Typically the need for faster line speeds has provided the impetus for tension regulation. The paper industry is a good example. In these industries the STR algorithm could easily be employed to tune up tension regulators in continuous process lines if the line speed is reduced during the tuning algorithm’s execution. No waste of material would occur.
Mill management systems provide a medium through which controller configurations for particular set-ups may be stored. Using such a management system would alleviate the need for initiating self-tuning for previously run product set-ups. In addition the self tuning algorithm need not be initiated for every product set-up, but rather for those where there is a significant change in product parameters or a predetermined error measure is exceeded.
The step stimulus used in the simulation may not be practical for most systems. For example, materials such as steel do not stretch much and a very little change in speed results in a significant change in tension. For these systems significantly smaller random speed steps would be required. If the system is employed without a speed minor loop, the step stimulus may be applied directly to the current reference and the resulting FFT would not include the speed loop. The use of a speed intermediate loop has been the subject of much controversy in web handling systems. Some industries, such as film and plastics, demand it. In other industries, such as steel and paper the split between the two tension regulation approaches is about 50-50. One of the objectives of Section 2 was to provide an understanding of what effect the inclusion of a speed intermediate loop has on tension regulation. This effect was summarized in the concluding remarks of Section 2.
Should the situation arise where a regulation scheme must be devised for a system where the plant dynamics are not well known, Anstaklis and Gao [2] describe an algorithm whereby the order of the controller can be determined iteratively based on a user defined set of constraints. This method would be very useful for the development of a generic STR compensator and could easily be litmus tested with a simulation similar to that presented in this paper. It would be interesting to compare regulation with STR tuned regulators using regulator structures obtained using the algorithm described in [2] with STR tuned regulators of lesser and greater order.
This paper did not investigate the use of frequency weighting in which is also discussed in [2] and [3]. Use of this technique may prove useful in reducing the number of points required in the pseudoinverse. For any implementation in hardware a reduction in the number of points used in the pseudoinverse will result in a reduction in computation time. This is extremely desirable in large systems where computational resources are constrained and emphasis is on ever increasing sample rates. In addition, the time taken to find the least squares solution to the system of linear equations of a particular application can be identified. Once identified system computational resources may be allocated in a predictable manner.
In conclusion, the evident elegance and straightforward implementation of the STR algorithm presented in this paper shows great promise for its application in contemporary industrial control engineering practice. It is in no way limited to the tension problem presented, but may be applied to any of a number of SISO control applications.
BIBLIOGRAPHIC REFERENCES
[1] Goderdhansingh, L. Wang and W.R. Cluett, "Robust Control System Design Using Direct Frequency Response", Proceedings of the American Control Conference pp. 3026 - 3030, June, 1992.
[2] P.J. Anstaklis and Z. Gao, "Polynomial and Rational Matrix Interpolation: Theory and Control Applications", International Journal of Control, Vol. 58, No. 2, pp 349-404, 1993.
[3] Z. Gao and P.J. Anstaklis, "New Methods For Control System Design Using Matrix Interpolation", Proceedings of the 33rd IEEE Conference on Decision and Control, pp. 2506 - 2511, December. 1994.
[4] Z. Gao, "An Algorithmic Approach To Loop Shaping With Applications To Self-Tuning Control Systems", Proceedings of the 8th. IEEE Symposium on Intelligent Control, August. 1993.
[5] A. P. Tzes and S. Yurkovich, "On Frequency Domain Loop Shaping For Self-Tuning Control", Proceedings of the American Control Conference pp 61 - 65, June, 1992.
[6] W.C. Carter, "Reducing Transient Strains in Elastic-Strip Processes", Control Engineering, pp. 84 - 87, March 1965.
[7] F. Parant, C. Coeffler, C. Lung, "Modeling of Web Tension in a Continuous Annealing Line", Iron and Steel Engineer, pp. 46 - 49, November, 1992.
[8] B. T. Boulter, J. Haboustak, "Accumulator Tension Regulation at Bethlehem Steel Corp. No. 4 HDCL", Systems Engineering Report No. 187, Reliance Electric Corporation Systems Division, May 1993.
[9] E. Cunningham, "Digital Filtering", Ch. 6,8 and 9, Houghton Mifflin, 1992.
[10] A. H. Whitfield, "Transfer Function Synthesis Using Frequency Response Data", International Journal of Control, vol. 43, No.5 pp. 1413-1426, 1986.
[11] Matlab Reference Guide, The Mathworks, pp.369 - 370, August 1992.
[12] K. J. Astrom, T. Hagglund, C. C. Hang, W. K. Ho, "Automatic Tuning and Adaptation for PID Controllers - a Survey", Control Engineering Practice, Vol.1, No.4, pp. 699 -714, August. 1993
[13] K. J. Astrom, B. Wittenmark, "Adaptive Control", Allison Wesley, 1989.
[14] G. M. Jenkins and D. G. Watts, "Spectral Analysis and Its Applications", Holden-Day, 1968.
[15] Z. Gao, B. Tabachnik, R. Savescu, "Transfer Function Matrix Identification From Input-Output Measurements", to appear in the Journal of the Franklin Institute.
[16] K. J. Astrom, "Autonomous Controllers", Control Engineering Practice, Vol.1, No.2, pp. 227 -320, April 1993.
[17] I. D. Landau, "Evolution of Adaptive Control", Journal of Dynamic Systems, Measurement and Control, Transactions of the ASME Vol. 115, No. 2B, pp 381 - 391, June 1993.
[18] L. Ljung, "MATLAB System Identification Toolbox", The Mathworks, August 1992.
[19] R. S. Shirley, "Some Lessons Learned Using Expert Systems for Process Control", IEEE Control Systems Magazine, pp 11 - 15, December 1987.
[20] K. G. Shin, X. Cui, "Design of a Knowledge-Based Controller for Intelligent Control Systems", IEEE Transactions on Systems, Man, and Cybernetics, Vol. 21 No.2 March/April 1991.
[21] C. C. Lee, "Fuzzy Logic in Control Systems -Part I and II", IEEE Transactions on Systems, Man and Cybernetics, Vol. 20, No.2 , pp 404-435 March/April 1990.

Figure 1. Proposed STR Scheme

Figure 2. The Physical Plant

Figure 3. The Plant Block Diagram (Including Web-Damping and Viscous Friction)

Figure 4. A Typical Non STR Web Tension Regulation Scheme As Used In Industry Today

Figure 5. Proposed STR Regulation Scheme (As Implemented In Simulation)

Figure 6. Theoretical Freq. Resp. (A = 0.1 [cm^2])
Figure 7. Estimated Freq. Resp. (A = 0.1 [cm^2])

Figure 8. STR Tuning (A = 0.1 [cm^2])

Figure 9. Theoretical v’s On-Line Tuning (A = 0.1 [cm^2])

Figure 10. Comparison of PI Regulation and STR Regulation (A = 0.1 [cm^2])
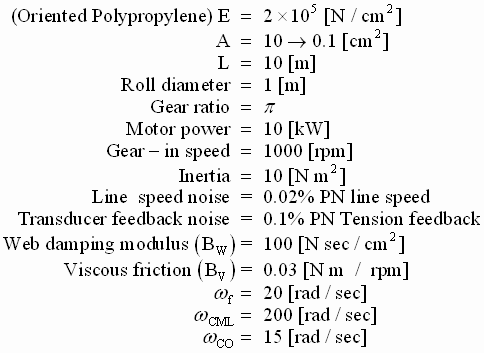
Table 1. Simulation Set-up Parameters
|