APPLIED INDUSTRIAL CONTROL SOLUTIONS
ApICS LLC
Air-Propelled People-Mover Vehicle
Speed Control System Analysis & Design
Brian T. Boulter
© ApICS ® LLC 2000
ABSTRACT
A computer model of a proposed air-propelled people-mover vehicle project in Florida is developed and a control system for controlling Vehicle speed is presented. Computer models were developed for the Vehicle dynamics, PPU (Propulsion Power Unit) blower characteristics, and air duct pressure. Also included are simulations of performance on hills, and the use of valve angle control and on-board Vehicle static braking systems for speed trim during deceleration. Fan motor torque calculations are included to provide information on expected torque loading and for calculating resulting stresses to the fan blades during normal operation.
INTRODUCTION
Scope
This report presents the results of simulating the Air-propelled people-mover Vehicle propulsion and control system. Computer models were developed for the Vehicle dynamics, blower characteristics, valve characteristics, on-board Vehicle braking systems, and air duct pressure. The purpose of the study is to identify a control strategy for automating the regulation of Vehicle speed, and provide guidelines for Vehicle positioning methods at stations. The goal is to negate the need for an operator while providing a comfortable ride for the passengers. Another goal of the report is to identify the dynamics of dual push/pull PPU systems, especially with respect to large changes in Vehicle loading, and non-level terrain.
Report Overview
This report contains detailed descriptions of the first principal equations used to describe the people mover Vehicle, PPU’s, Propulsion Duct, and the proposed regulators using the PPU’s planned for use in the Florida installation. The model detail is adequate enough to facilitate the identification of a proposed control strategy that is hoped will provide a fairly simple and easy to start-up control solution for regulating Vehicle speed in these applications.
The control solution presented in the simulation is implemented with fully functional Simulink S-Function models of existing Distributed Control System (DCS) blocks. The S-Functions were designed to reflect the behavior of a DCS control solution, they use the same difference equations that are used in DCS Blocks. The simulation is therefore truly dual mode, with the plant simulated using continuous mode models, and the controllers simulated using discrete mode models. The resulting hybrid simulation is able to accurately model the effects of sample time and algorithm computation times on control loop phase margin. The DCS representation also includes programmed limiting and clamping functions that limit the response of sub-systems to those achievable in the real application. This makes the simulation results more reflective of the anticipated response of the control loops, than the overly optimistic results that would be obtained in a fully continuous model, without limits.
Sequencing has been included to model the proposed drive configuration during acceleration, run and deceleration. The sequencing is structured so that the Vehicle speed during acceleration and run is controlled through the force applied to the Vehicle sails with propulsion tube pressure via the PPU fan blower speeds. During deceleration the Vehicle speed is controlled with both the brakes on the Vehicle and the duct pressure, which is regulated by a valve aperture opening, rather than the fan speed.
The report is divided into 6 sections. The first section contains a table of contents, the list of illustrations, the abstract and this introduction. The second section (Chapter 1) contains a detailed overview of the design specifications for the project, vendor supplied descriptions of the equipment to be used, including motor characteristics, blower characteristics, valve characteristics, and Vehicle specifications. The third section (Chapter 2) contains descriptions of the principal equations describing the plant, and a functional description of the DCS blocks used in the design and simulation of the controllers. The fourth section (Chapter 3) contains a detailed functional description of the simulation block diagrams, and the feed-forward and feedback control strategies employed.
The fifth section (Chapter 4) contains simulation results for station to station runs under loading conditions varying from an empty Vehicle to a fully loaded Vehicle. The simulated runs are also performed for various terrain configurations. The results include plots of Vehicle reference and feedback speeds, Propulsion Duct pressures, PPU blower speeds, and PPU Blower shaft torques. The sixth section (Chapter 5) summarizes principal observations and presents a series of conclusions. Following is a more detailed description of the contents of the Results chapter.
Observations/Conclusions
The process of modeling and simulating the proposed Air-propelled people-mover control scheme provided the author with the following insights:
- The phase lag associated with the transport delay in the propulsion tube, limits the responsiveness of the Vehicle Speed regulator. Deploying a modern control based Vehicle speed regulator (for example a regulator with a smith predictor, designed with an accurate plant model) will only improve response to a command reference, it will not improve response to a disturbance. The same response to a command reference can be achieved in a much simpler fashion using feed-forward pressure references. Implication: To reduce complexity, and optimize response to a command reference, use a simple speed regulator with pressure feed-forward control.
- To position the Vehicle at a station, an approach similar to that used in the elevator industry should be employed. That is: Accelerate the Vehicle to the desired cruise speed, and monitor position. When the Vehicle reaches a pre-determined position on the track decelerate to a "Leveling speed". Once at the desired leveling speed (usually a very low speed), the Vehicle coasts for a short time until reaching the desired station stop point at which time the brakes are fully applied and the Vehicle is stopped. Implication: Disturbances such as wind, earthquakes, tidal waves etc. will generate an error in the Vehicle final position. To compensate for these disturbances an intelligent positioning algorithm can be closed around the Vehicle brakes, in much the same way the Vehicle is currently positioned. Alternatively, an algorithm that corrects the speed reference to accommodate for these disturbances can be developed, but is not presented in this report.
- To accelerate the Vehicle from stop to coast speed while satisfying the design constraints, the fan must be accelerated using 250% rated torque for as much as 10 [sec]. AC and DC motors can be designed to operate with this load torque for short periods of time. Care should be taken to ensure that motors are chosen with frames designed to handle these loads for the expected application duty cycle times.
- Care should be taken to ensure that physical limits are programmed into the regulators correctly, and that once a limit is reached all integrators in the control loop are clamped. This prevents wind-up in the integrators. For the pressure regulators, it may become necessary to program limits that vary with air mass-flow, and are based on the particular PPU blower characteristics.
- The proportional pressure regulator that is closed around the Fan speed regulator (during acceleration and run) will operate with a fixed steady state error that varies depending on the air mass-flow through the blower. To compensate for this steady state error a slow integrator was added to the Vehicle speed loop. This integrator should only be given as much control as the application requires.
- Acceleration and deceleration rates for the speed reference generator should be computed (or generated in a look up table) based on the Vehicle mass, and the worst-case analysis of available pressure, for a given PPU configuration.
- The Blower-Fan motors were observed to regenerate during the simulations. If a non-regenerative drive is to be used, care should be taken to ensure that the snubbers are sized adequately to absorb the expected regenerative energy, within the constraints imposed by the worst-case duty cyle of the Vehicle.
Minimizing Anticipated Start-up Difficulties3
To minimize difficulties during start-up, the author feels that care should be taken to ensure that the following tasks are performed correctly.
- Ensure that each PPU fan speed regulator is tuned for a 1 [rad/sec] loop bandwidth.
- For each PPU, ensure that the pressure loop (into fan speed) is tuned for a bandwidth of approximately 1-2 [rad/sec].
- For each PPU, ensure that the pressure loop (into valve position) is tuned for a bandwidth of approximately 1-2 [rad/sec].
- For each PPU, ensure that the feed-forward pressure references and the associated switch points are adjusted so that the Vehicle operates within design guidelines without closing the Vehicle speed regulator.
- For each PPU, ensure that the Vehicle speed regulator is tuned for approximately 0.1 – 0.2 [rad/sec] bandwidth.
This concludes the report.
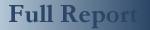
|